Understanding Porosity in Welding: Exploring Causes, Effects, and Avoidance Techniques
As professionals in the welding sector are well aware, understanding the reasons, impacts, and prevention techniques related to porosity is critical for attaining robust and reputable welds. By diving right into the origin creates of porosity, analyzing its destructive results on weld quality, and discovering reliable prevention approaches, welders can enhance their expertise and abilities to produce top notch welds regularly.
Common Root Causes Of Porosity
Contamination, in the form of dust, oil, or corrosion on the welding surface area, produces gas pockets when heated, leading to porosity in the weld. Incorrect securing happens when the shielding gas, generally made use of in procedures like MIG and TIG welding, is unable to totally safeguard the liquified weld pool from reacting with the bordering air, resulting in gas entrapment and subsequent porosity. Furthermore, inadequate gas coverage, typically due to wrong circulation prices or nozzle positioning, can leave parts of the weld unsafe, permitting porosity to create.
Effects on Weld High Quality
The visibility of porosity in a weld can dramatically compromise the total high quality and stability of the welded joint. Porosity within a weld creates spaces or dental caries that deteriorate the framework, making it a lot more prone to cracking, rust, and mechanical failure. These spaces act as stress concentrators, reducing the load-bearing ability of the weld and increasing the likelihood of early failing under applied tension. Additionally, porosity can also act as prospective sites for hydrogen entrapment, additional aggravating the deterioration of the weld's mechanical properties.
Additionally, porosity can prevent the effectiveness of non-destructive screening (NDT) techniques, making it testing to spot various other issues or suspensions within the weld. This can cause substantial safety concerns, particularly in crucial applications where the structural stability of the bonded parts is critical.
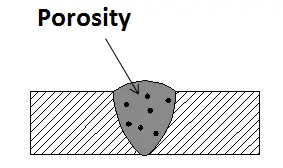
Prevention Techniques Review
Given the damaging effect of porosity on weld top quality, reliable prevention methods are crucial to keeping the structural stability of welded joints. In addition, picking the appropriate welding criteria, such as voltage, existing, and take a trip rate, can help decrease the threat of porosity formation. By integrating these prevention methods right into welding techniques, the occurrence of porosity can be significantly reduced, leading to stronger and a learn this here now lot more trustworthy bonded joints.
Importance of Correct Shielding
Appropriate securing in welding plays a crucial role in preventing atmospheric contamination and making certain the stability of welded joints. Shielding gases, such as argon, helium, or a mixture of both, are frequently made use of to secure the weld pool from responding with components in the air like oxygen and nitrogen. When these reactive components come into contact with the warm weld swimming pool, they can trigger porosity, resulting in weak welds with minimized mechanical buildings.
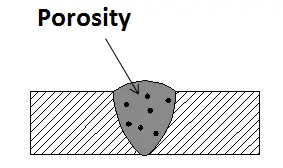
Poor protecting can result in numerous defects like porosity, spatter, and oxidation, endangering the structural honesty of the welded joint. Sticking to proper shielding techniques is crucial to create premium welds with very little issues and make certain the longevity and dependability of the bonded components.
Tracking and Control Approaches
Exactly how can welders efficiently check and regulate the welding procedure to guarantee optimum outcomes and avoid issues like porosity? By constantly keeping track of these variables, welders can determine inconsistencies from the excellent conditions and make instant adjustments to stop porosity development.

In addition, applying proper training programs for welders is necessary for checking and managing the welding process efficiently. What is Porosity. Educating welders on the value of maintaining constant parameters, such as correct gas shielding and take a trip rate, can aid protect against porosity issues. Regular evaluations and qualifications can likewise guarantee that welders excel in surveillance and managing welding processes
Furthermore, making use of automated welding systems can enhance monitoring and control abilities. These systems can specifically manage welding parameters, reducing the probability of human mistake and guaranteeing consistent weld high quality. By combining sophisticated surveillance innovations, training programs, and automated systems, welders can successfully check and control the welding process to lessen porosity issues and attain high-grade welds.
Conclusion
